The best insurance cover, well, ever
We secured insurance rates with our global partners and pass off the peace of mind to you and your customers. The most competitive insurance rates in e-commerce that also offset our planet’s carbon. Win, win.
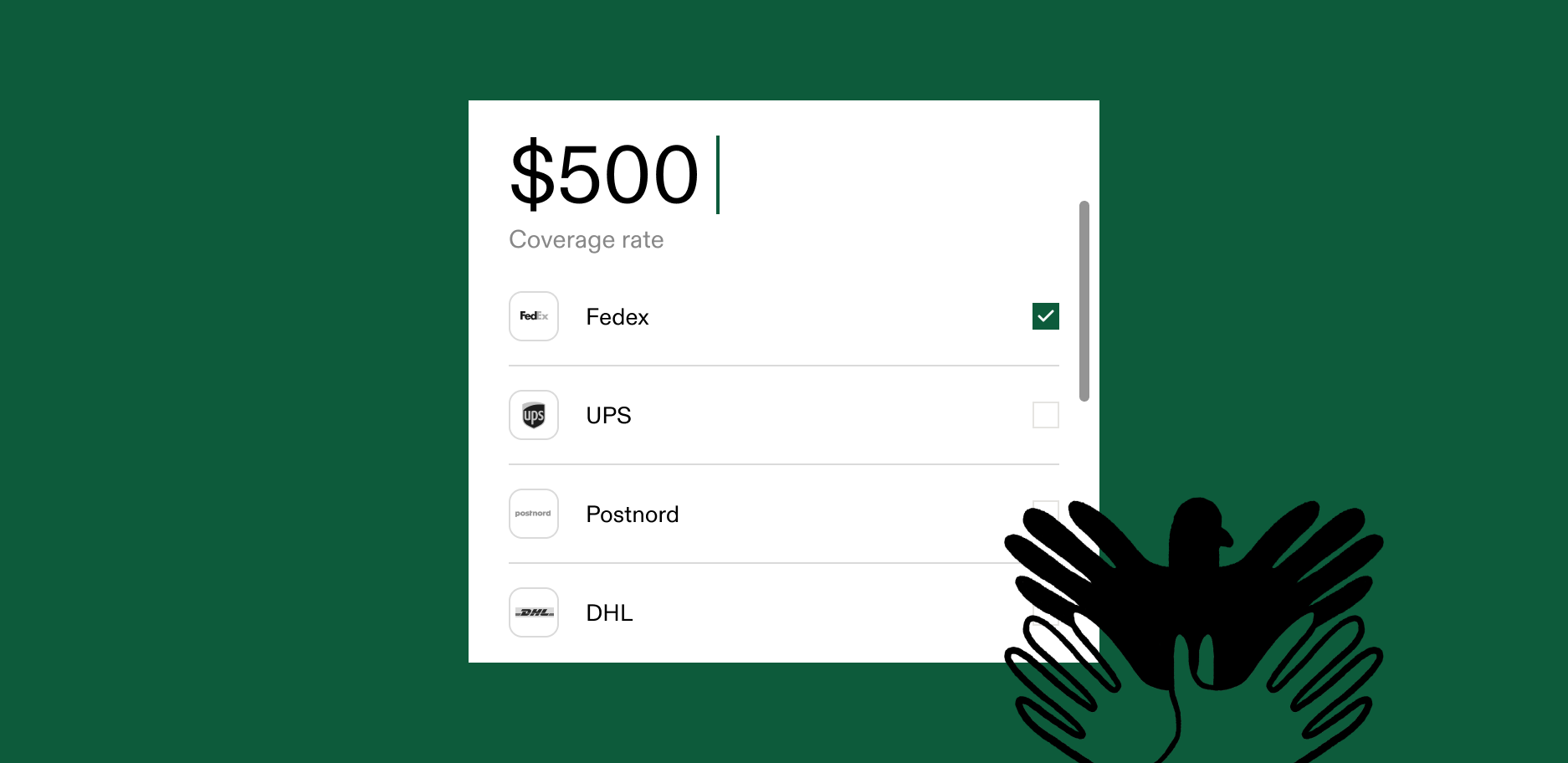
We’re not chefs, but we know how to bake it in.
Get every order fully insured with our global carriers. Set your coverage rate automatically baked into the cost, activate it, and watch those orders fly in.
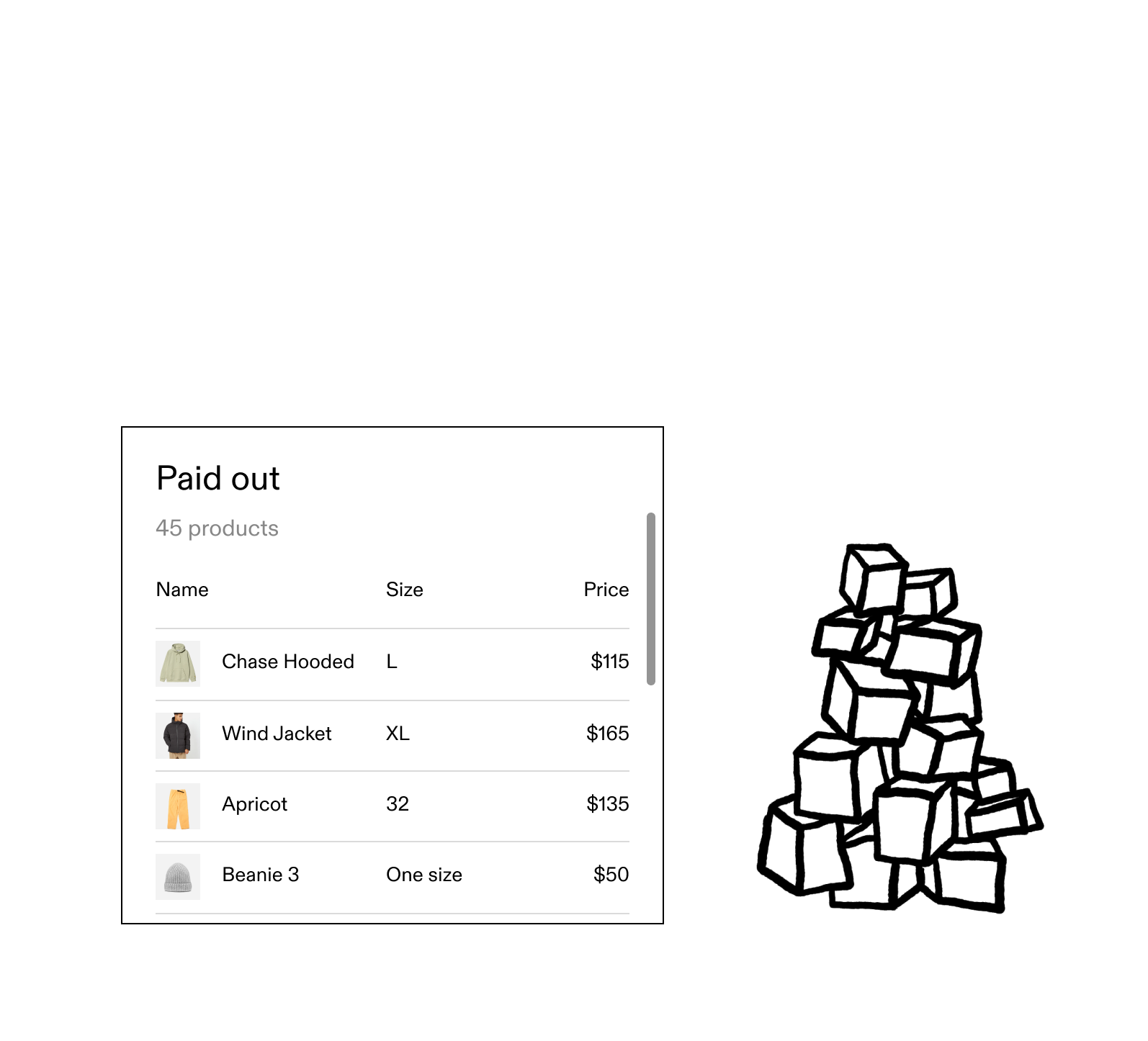
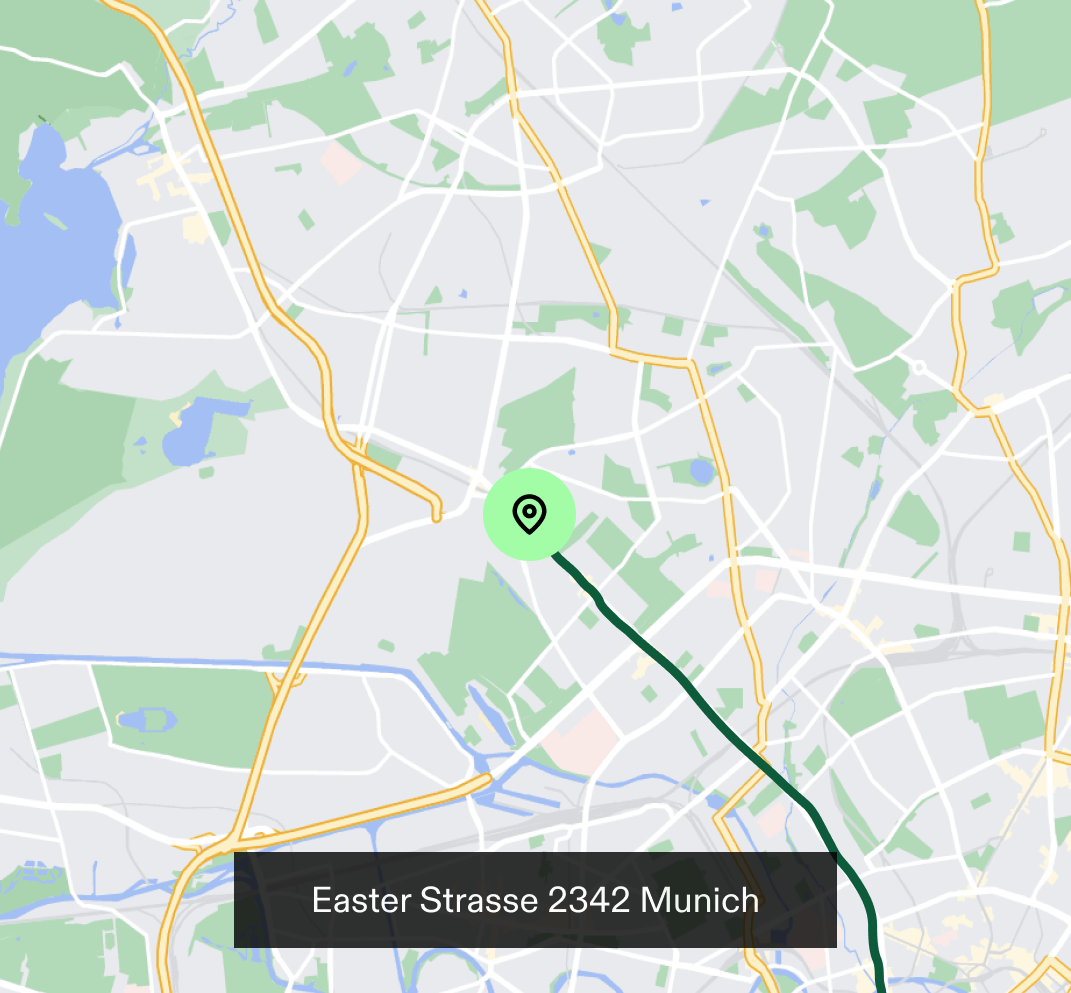
Door-to-door coverage
We’ve got our eyes on your items at all times, which means you'll never again have to refund a customer because of a lost, damaged, or missing package.
Stay on top of the flock.
Subscribe to get the latest from the ecommerce operating system that reduces your tech stack to one login.